I fabricated the 0.020″ spacers for the hinges that attach the bottom of the cowl to the firewall.
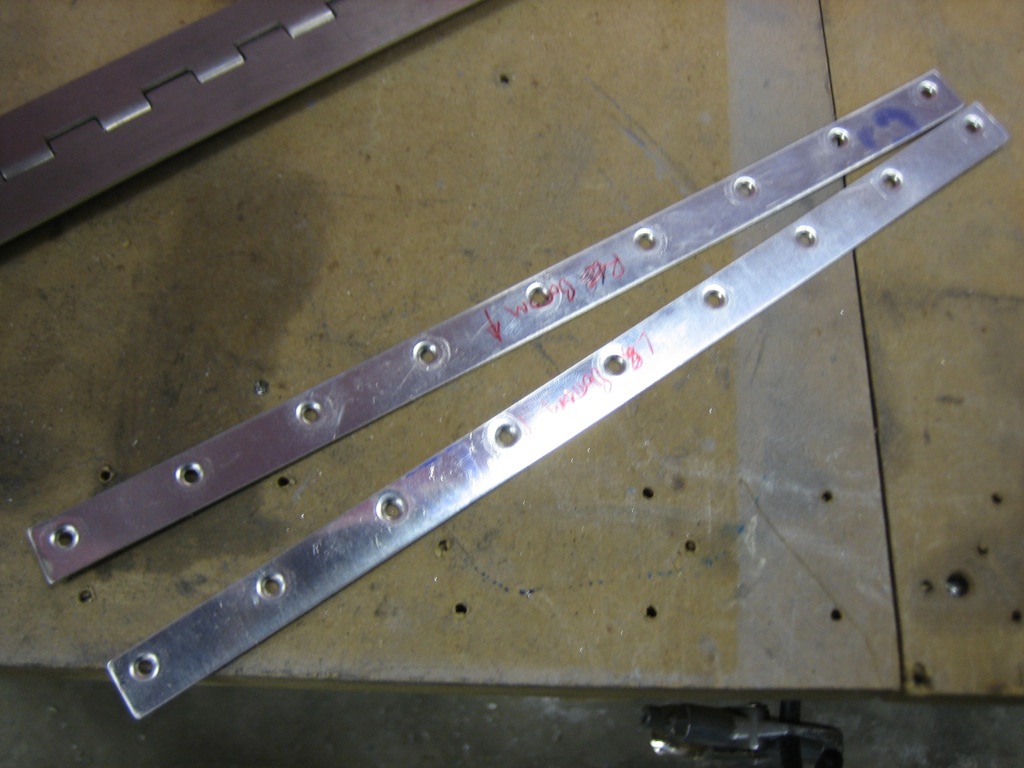
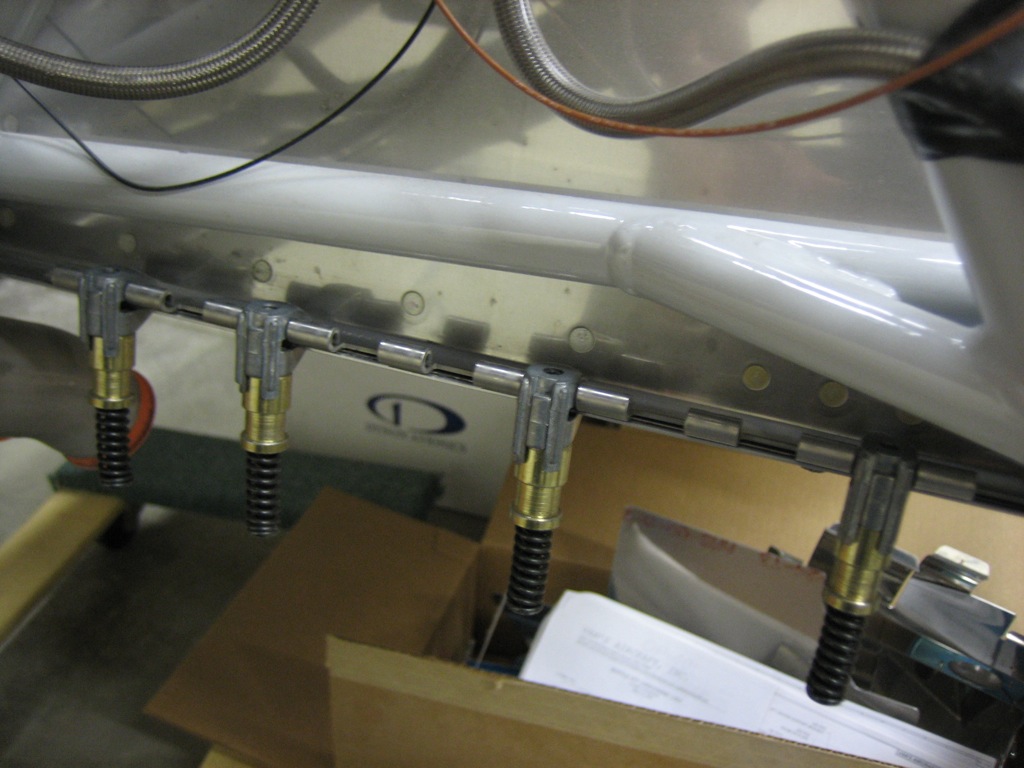
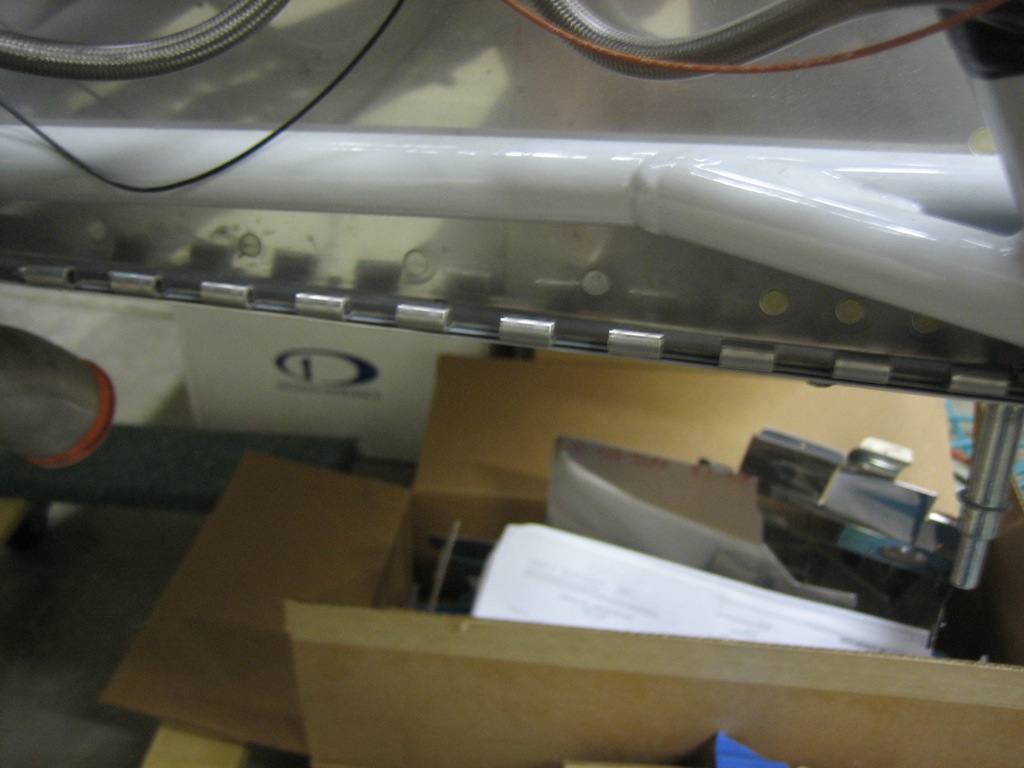
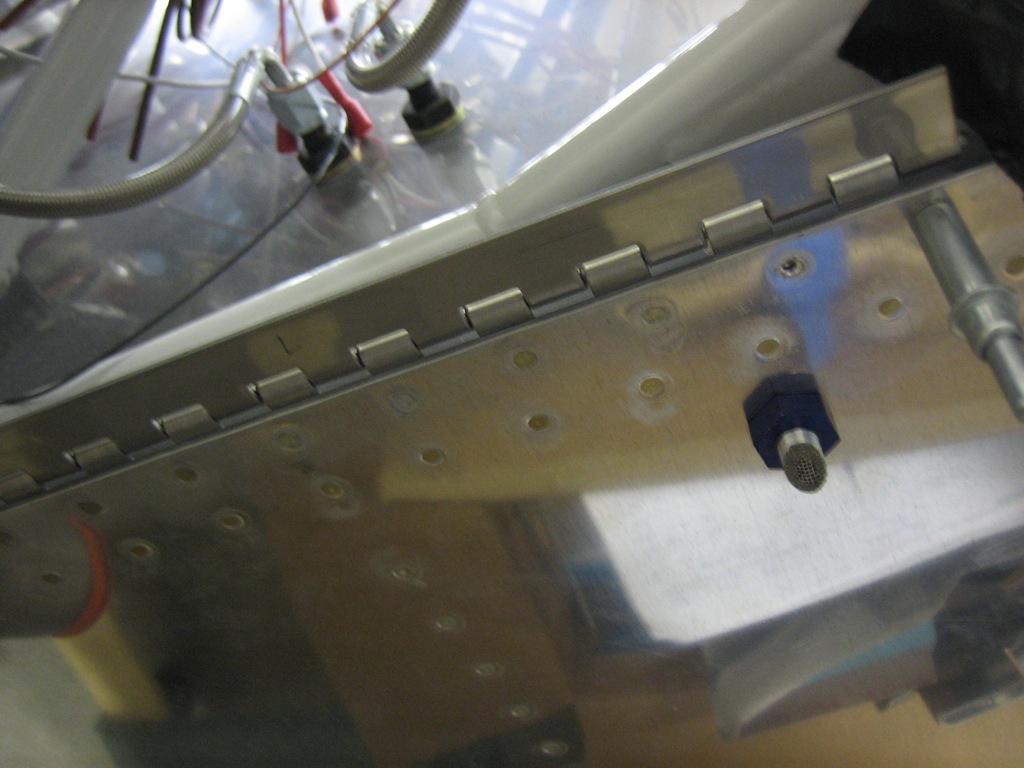
I fabricated the 0.020″ spacers for the hinges that attach the bottom of the cowl to the firewall.
The throttle bracket that I mocked up a couple of days ago had an extra bend that was unnecessary and I couldn’t figure out how to bend it using the tools I have. Instead, I mocked up a simpler bracket. The slot on the end was only to make it easier to fit while mocking it up.
I unfolded the prototype and transferred it to a piece of 16 gauge steel.
I marked out the bends and bent them using this vise brake that I borrowed from my dad. This thing had no problems bending 16 gauge steel.
I drilled the mounting and cable holes and temporarily mounted it to the engine. Unbelievably, I absolutely nailed it on the first try. The 1/4″ mounting holes perfectly lined up with holes on the sump and the placement and angle of the cable hole was spot on.
Here’s a closeup of the mounting end. This picture makes it look like it comes pretty close to the exhaust pipe, but there’s quite a lot of clearance.
After some adjustment, here’s the throttle in the full open position. Notice the slight gap between the nut behind the throttle nob and the friction control. This ensures that the throttle arm hits the stop on the fuel injection servo which ensures that you can reach full throttle.
Here’s the throttle in the full closed (idle) position. Again, I’m hitting the stop on the fuel servo which ensures I’ve got the throttle fully closed.
This is a poor picture, but it shows the alignment between the throttle cable and the hole in the firewall. It’s a perfectly straight shot back to the firewall from the bracket and clears the heat muff inlet by a 1/2″ or so.
Now that the throttle bracket fits correctly, I can clean it up and powder coat it before installing it for good.
The stock throttle bracket that Van’s supplies doesn’t work with the Superior sump since the attach point is in a different location. I’m going to fabricate a custom bracket out of some 16 gauge steel (the same thickness as Van’s bracket). I used some really thin (0.004″) aluminum flashing I had on hand to mock up the bracket. This puts the cable on a direct path to the hole in the firewall and keeps it well clear of the exhaust and sump.
Here’s a shot from slightly lower in case that makes it more clear.
Here’s what the rough bracket looks like. I unfolded this and traced the pattern onto some 16 gauge stock I picked up from Home Depot. Cutting it out will be easy, but I’m still not quite sure how I’m going to bend this.
I installed the exhaust stabilizer strap that ties the two pairs of exhaust pipes together. This significantly stabilizes the exhaust pipes over just having each pair supported by on hanger.
Construction work is slowing down on the plane a bit while I’m working on the electrical system design. The VP-X is fairly significantly different than the architecture specified in the Aeroelectric Connection. I’m reworking most of the schematics and still trying to decide how I’m going to handle backup circuits for several devices.
Dynon and Vertical Power this morning announced that the SkyView system will be supporting the VP-X. After seeing the VP-X at Oshkosh last year, I decided to defer working on the electrical system as long as possible in the hopes that this will happen. Thanks guys; this combination is going to rock!
Here’s the announcement from Dynon:
http://www.dynonavionics.com/docs/news_VPX_announcement.html
It’s a little disappointing that they’re charging an additional $275 for this given that they’ll almost certainly sell more SkyView systems as a result and because every other avionics supplier is including it for free. Dynon products are already priced much more aggressively than their competitors though, so I’m not going to complain too loudly.
Here’s an overview of the VP-X:
http://verticalpower.com/vp-x/
After working through the load planning, I’ll be going with the VP-X Pro. Using the VP-X should not only simplify wiring, it should provide substantial new features to the electrical system as well as advanced fault detection.
Now, if Garmin would just announce a replacement for the GNS-430…