When I did the first taxi test, I had incorrectly installed the screws that tie the conical section of the spinner backplate halves together. I forgot that there was a note in the installation manual that the screw heads needed to be on the aft side to provide clearance between the spinner and cowl. I installed the nut on the aft side, and the ends of the screws cut into the cowl flange a bit. I ground all of the damaged material out of the cowl and then applied a thin layer of raw epoxy to coat the inside of the cut. In addition to reversing the screws, I switched from AN515 to AN525 screws to further reduce the height of the head.
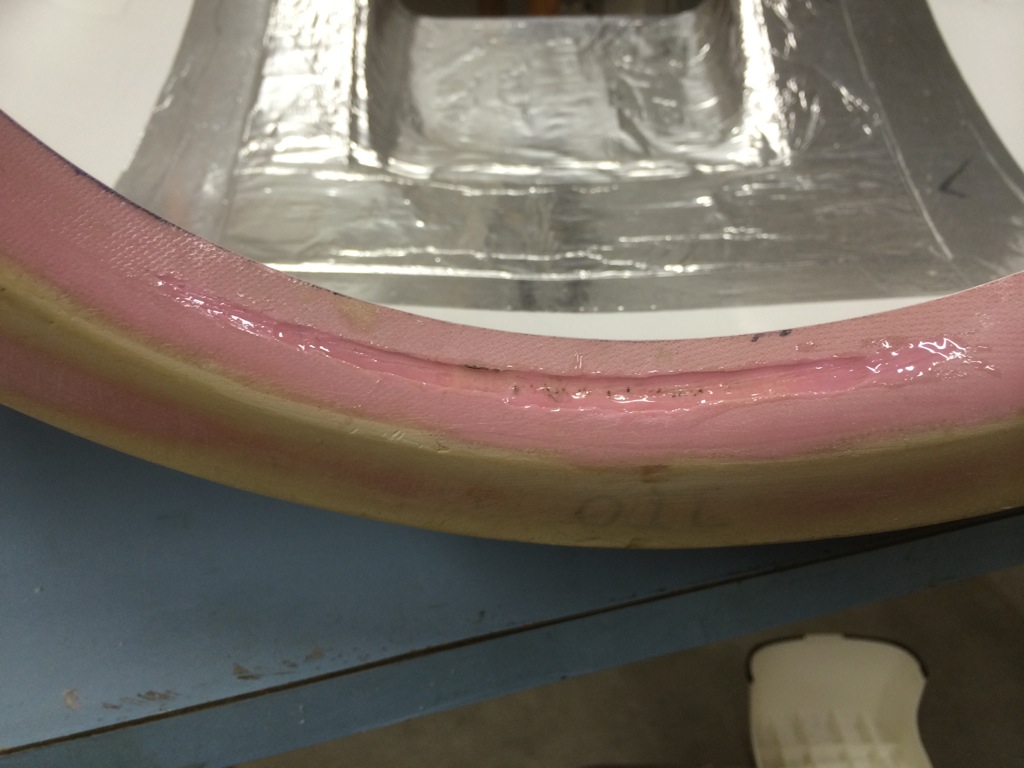
My flox is down at the hangar, so I cut up a small piece of fiberglass cloth into tiny pieces and mixed it into some epoxy. I filled the gap with this and left it a little proud of the surface. I’ll grind this flat once the epoxy cures.
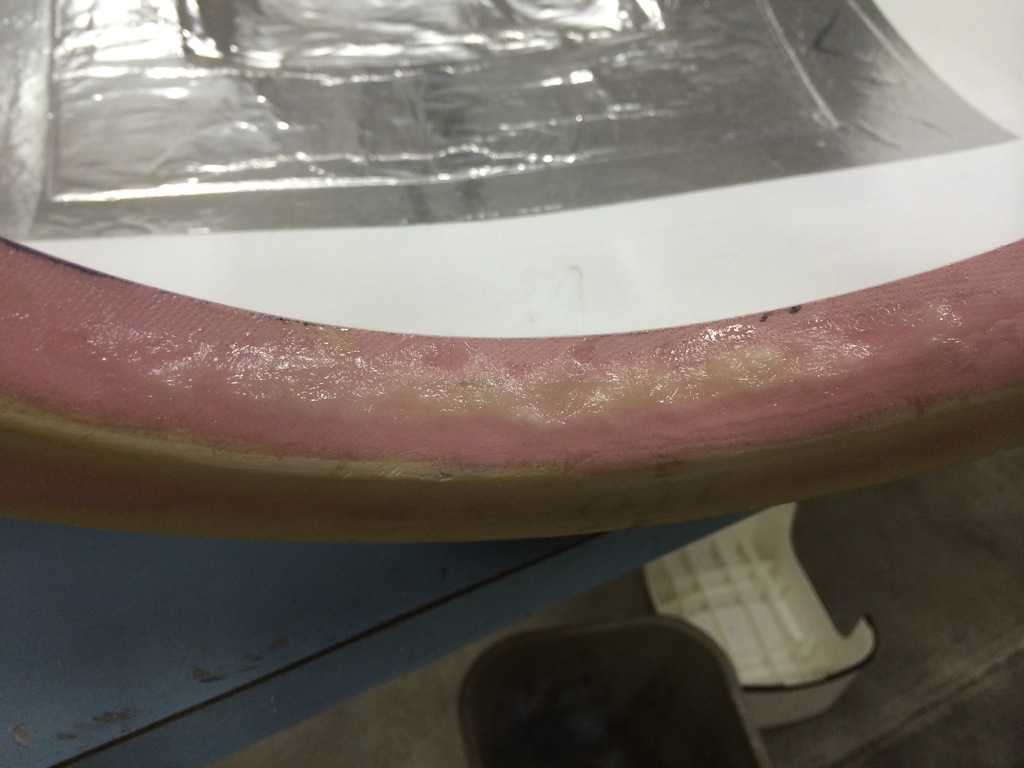
While the epoxy was curing, I sanded both cowl air inlet on the top and bottom. The cowl is very close to getting the first coat of primer.
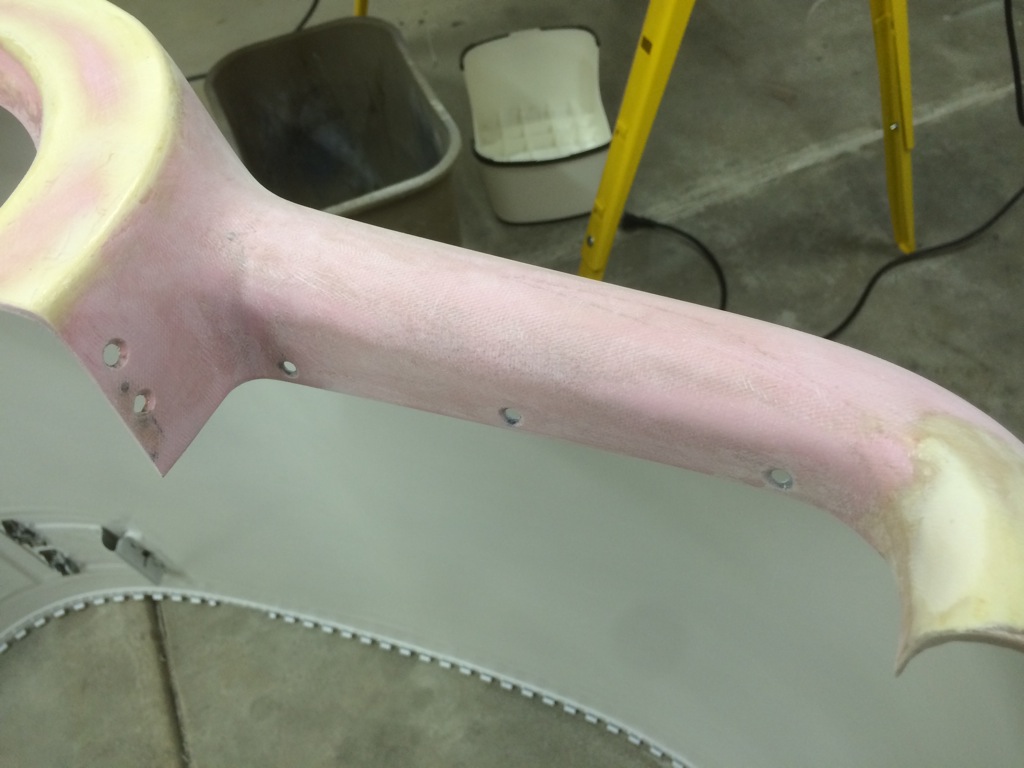