After reevaluating the shims I had made, I decided that using shims that varied in thickness was the wrong approach. The ribs already define the correct wing curvature, so shims that vary in thickness would just create ripples in the skin. The problem is really that the splice plate is too low and the variation I measured was due to the tank skin getting pulled tighter where the screws attach and pillowing out between them. Instead, the entire splice plate needed to be shimmed out a small amount. Looking at the measurements I made previously, I determined that shimming the splice plates out 0.016″ and shimming the skins out a further 0.008″ would be about right.
I fabricated the new set of shims using some 0.008″ aluminum flashing purchased from the aviation isle at Home Depot. Two will fit between the inboard rib and the splice plate and one will fit between the splice plate and the skin (the outboard skin is 0.024″ and the tank skin is 0.032″, so this should bring the skins flush).
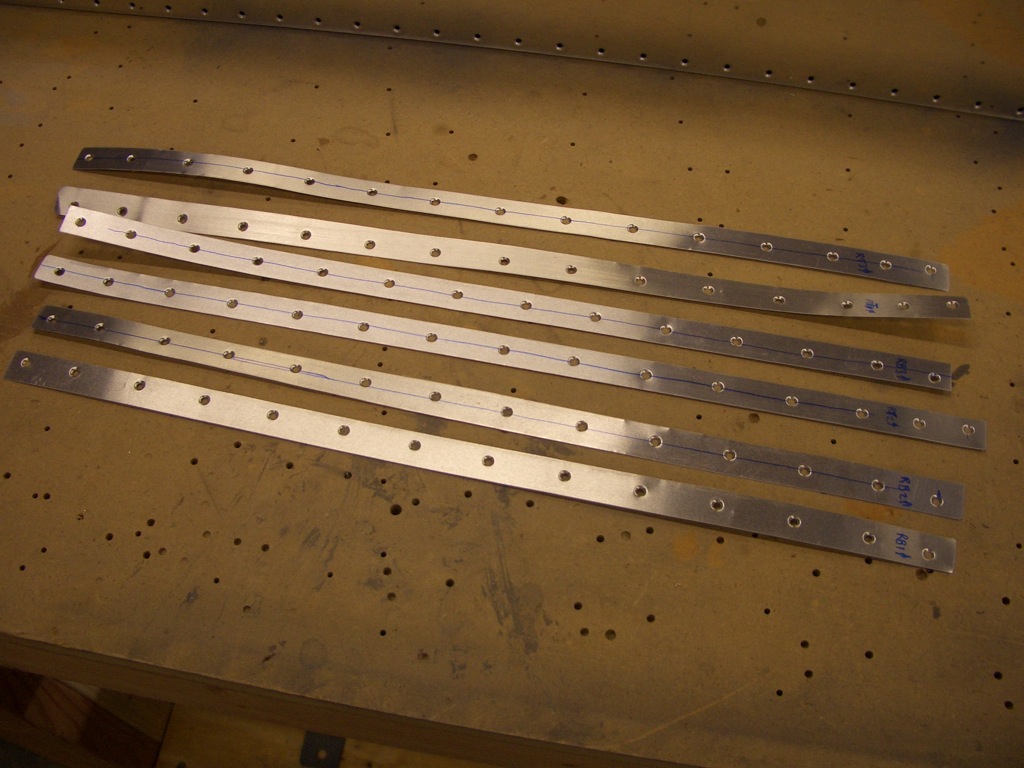
My wife Jenn helped me rivet on the rib (it was only her second time riveting, and she did a fantastic job). The fit was nearly perfect right after installation. I did a little adjustment, and now the tanks and outboard skins are flush to within a few thousandths pretty much the whole length of the joint.